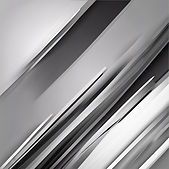
SAFE-FIRE NEWS 2019 Q2


USER FEEDBACK
SAFE-FIRE IGNITION SYSTEM AND FLAME DETECTION SYSTEM OPERATING SMOOTHLY
Safe Fire Ignition System and Flame Detection System were retrofitted into Unit #4 of Baoshan Steel Ltd. Power Plant. The boiler is a 350MW Opposed-Fire boiler manufactured by Babcock and Wilcox. Prior to the retrofit project, the plant suffered from equipment not being able to detect flames due to 4 different types of fuels were used. The plant also experienced difficulties in ignition when start up the boiler. The plant had a successful boiler start up on July 24. The customer were very satisfied with the result of this retrofit project and they were able to achieve:
• An one-key programmable ignition start for the entire burner system
• Stable flame detection signals which enables safe operation.


PRODUCTS
TEMPVISION 5000 Temperature Profile Measurement System

Safe-Fire’s TempVision-5000 system continuously measures – in real time – burner flame temperature profiles inside a boiler or furnace combustion chamber. This dynamic system can be configured for use on a variety of boilers and furnaces with the appropriate combination of TempVision Detectors and a processing/ communications suite. The on-demand combustion temperature display enables plant operators to make informed decisions to adjust the crucial fuelto-air ratio inside the furnace. With a focus on the combustion field, Safe-Fire is committed to improving our customers’ combustion efficiency through reduced fuel consumption, decreased emissions, and increased boiler service life.
FEATURES
• Dual-spectrum imaging technology
• Temperature measurement range 850 °C to 1900 °C
• Accuracy of measurement 1%
• Excellent resistance to dust interference

USER INTERFACE
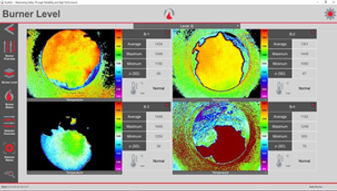

SYSTEM DIAGRAM

PROJECT
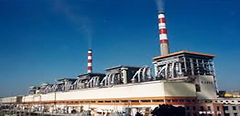
POWER PLANT:
Zouxian Power Plant
600MW, UNIT#6,
Shandong, CHINA
BOILER MAKER:
Foster-Wheeler Energy Co.
Safe-Fire completed the installation of a 24-Detector TempVision5000 System at Zouxian Power Plant Unit #6. The boiler is a 24 low-NOx coal burner opposed-fired boiler manufactured by Foster-Wheeler Energy Co. The project scope included engineering design, equipment supply, installation guidance, system commissioning, combustion adjustment and on-site training. The TempVision 5000 system installed performs real-time burner temperature profiling for the boiler, and provides plant operators with accurate burner temperature distribution data so they can make effective adjustments to improve combustion efficiency. By balancing the temperature distribution, operators can reduce
coal consumption, slagging and emissions.


CONTRACT PERFORMANCE KPI:
• Improve boiler efficiency by 0.5%
• Same level burner temperature differential less than 80°C
2. TempVision 1000 for Combustion Tunning for Wuxi Rong Cheng Paper Co. LTD.

Safe-fire TempVision 1100 improved efficiency by 2.85% and lowered fuel consumption by 2.46% at Wuxi Rong Cheng Paper Co. Ltd.

POWER PLANT: 220t/h Boiler, Wuxi
Rong Cheng Paper Co. Ltd., China
BOILER TYPE: Tangentially Fired Boiler
In June 2019, Safe-fire service team collected temperature data using TempVision1100, followed with a combustion tuning for boiler Unit #3, a 220 t/h capacity Tangentially fired boiler. The measurement data revealed that the combustion in certain areas of the furnace were unstable, and the combustion temperature fluctuated greatly. Based on the data, the team adjusted the secondary air of the boiler. The data collected after the tuning confirmed that the temperature fluctuation was significantly improved.

1. TempVision 5000 System in Operation at Zouxian Thermal Power Plant

APPLICATION
1. TempVision 1000 Reduced Coal Consumption by 3.25% for Opposed-Fire Boiler

POWER PLANT: Power Plant, Turkey, 600MW, Opposed-fire
BOILER MANUFACTURER: Dongfang Boiler Works, China
BURNERS: Front Wall 12, Rear Wall 12
COAL TYPE: Bituminous Coal
TempVision 1000 captures and displays the temperature profile of each burner flame in real time. This versatile mobile enables technicians to accurately map the profile of any burner using any available opening at any level. Through reliable and precise measurements, TempVision-1000 is the cornerstone in optimizing burner flame temperature distribution, which results in reduced fuel costs, NOx, and CO emissions.
It has been a challenge to obtain the temperature data of each individual burner for opposed-fire boilers. The temperature deviation of burners lead to inefficient combustion.

To collect the temperature profile of each burner, Safe-Fire’s fiber scope model TempVision 1000 was utilized. Through the outer carriers of the flame detector access on both the front and real walls, temperature profiles of all 24 burners were collected. The measurement data revealed that at some burner levels, the temperature variations
are as high as 145°C. In addition, the temperature data indicated an unbalanced combustion between front and rear wall of the boiler. Based on the temperature data, the team did a quick experimenting adjustment of the secondary air damper. This alone immediately deliv ered a result of a 3.25% decrease in coal consumption. This encouraging result suggests that an installation of an online TempVision System will benefit the plant greatly to reduce fuel cost, improve combustion efficiency, and enhance boiler safety performance.
2. TempVision 1000 Improves Combustion Efficiency for CFB Boiler

POWER PLANT: PLTU Kaltim Teluk Power Plant, Indonesia, 2x110MW, CFB
BOILER MANUFACTURER: Dongfang Boiler Works, China
BURNERS: Upper 4, Lower 4 COAL
TYPE: Lignite
TempVision 1000 captures and displays the temperature profile of each burner flame in real time. This versatile mobile enables technicians to accurately map the profile of any burner using any available opening at any level. Through reliable and precise measurements, TempVision-1000 is the cornerstone in optimizing burner flame temperature distribution, which results in reduced fuel costs, NOx, and CO emissions.


Maintaining the actual bed temperature to its design level helps to achieve fuel efficiency for CFB boilers. The boilers at PLTU Kaltim Teluk Power Plant, Indonesia, were CFB boilers manufactured by Dongfang Boiler Works. To collect the bed tempeature profile, Safe-Fire’s fiber scope model TempVision 1000 was utilized. Through the outer carriers of the flame detector access, temperature profiles of all 4 sets upper bed burners were collected.
Guided by the precise temperature data, the upper secondary air damper was adjusted. This immediately delivered a result of a 1.5% decrease in coal consumption which is a 0.76% combustion efficiency improvement.

3. TempVision 1000 Increase Fuel Efficiency for T-Fired Boiler

POWER PLANT: PLTU Pelabuhan Ratu Power Plant Indonesia, 3x350MW, T-Fired
BOILER MANUFACTURER: Shanghai Boiler Works, China
BURNERS: 20
COAL TYPE: LRC, MRC
TempVision 1000 captures and displays the temperature profile of each burner flame in real time. This versatile mobile enables technicians to accurately map the profile of any burner using any available opening at any level. Through reliable and precise measurements, TempVision-1000 is the cornerstone in optimizing burner flame temperature distribution, which results in reduced fuel costs, NOx, and CO emissions.
Combustion optimization is to properly distribute the fuel and air supply for control of NOx and manage the fine line between staged combustion and efficient
operation. Utilizing Safe-Fire’s TempVision 1000, burner flame temperature profiles were collected from Unit #1 of PLTU Pelabuhan Ratu Power Plant Indonesia, a Shanghai Boiler Works made T-Fired boiler. The temperature data clearly revealed the unbalanced combustion. The data also provided the guidance to tune the secondary air flow of the CD level on Boiler Unit #1. After the adjustments, the boiler load jumped from 308.4MW to 323.7MW, a 4.96% increase. This could potentially resulted in a 1.95% fuel savings at the plant, which is equivalent of about $1.44M monetary savings per year for this boiler unit only.
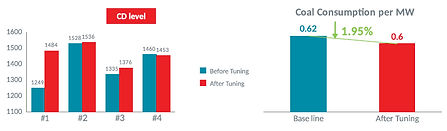